Matières premières du chantier, les matériaux mis en œuvre par les professionnels ne sont pas des ressources brutes. Ils ont vécu des transformations depuis leur site d’extraction avant d’être magnifiés par la main de l’ouvrier sur le terrain. Tuiles, ardoises, bois de charpente, pierre, chaux… Comment ces matériaux sont-ils produits à l’heure de l’industrialisation ?
Étudier les matériaux, c’est dérouler l’histoire de la construction, des pigments utilisés dans les grottes préhistoriques aux usines actuelles de ciment ou de tuiles. Liés à leur environnement, les matériaux du patrimoine sont, à l’origine, essentiellement, des produits locaux fabriqués régionalement afin d’en faciliter le transport. Aujourd’hui, les progrès de l’industrialisation et les effets de la mondialisation ont changé la donne.
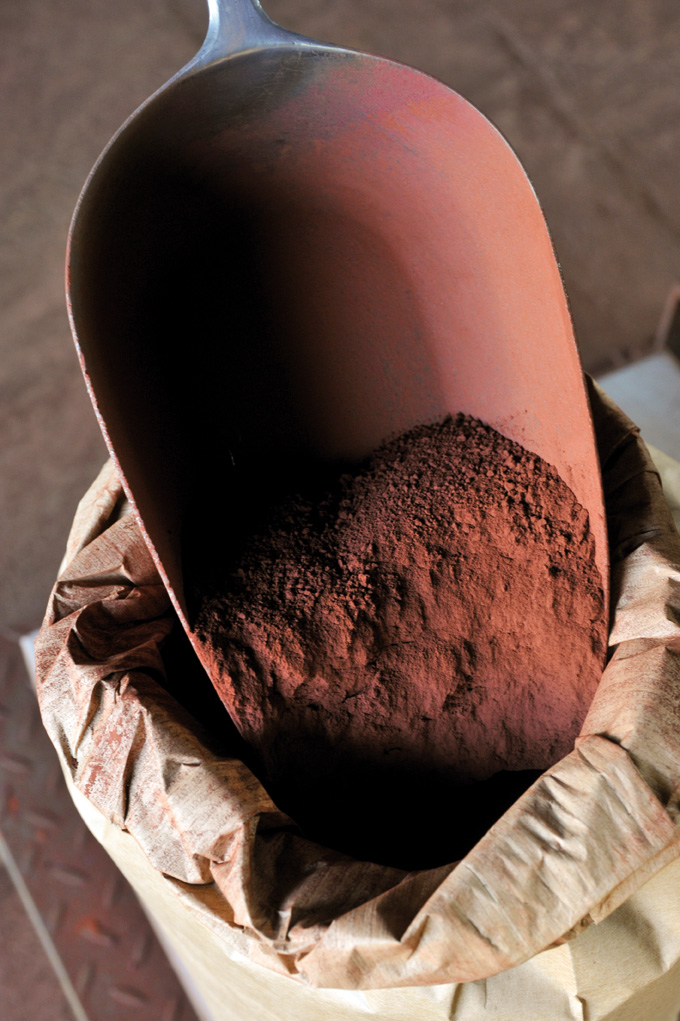
Dernière fabrique de terres colorantes en France, Le moulin à couleurs commercialise près de 80 références dont 45 pigments naturels parmi lesquels les ocres de France, la « terres de sienne » des Ardennes, les ombres naturelles et calcinées…
Photo : Le moulin à couleurs

Tuiles Aléonard réalisées selon une méthode traditionnelle : l’argile défile sur la filière, puis est découpée en tronçons avant cuisson.

Carrière à ciel ouvert, à Bierry-les-Belles-Fontaines, dans l’Yonne : le sciage de la pierre est assuré soit par des haveuses masses, soit par des machines à fil diamant et des perforatrices. L’équarrissage des blocs de pierre, s’il est nécessaire, sera effectué au moyen d’haveuses automotrices. La manutention des blocs est réalisée au moyen de chargeuses à fourche.
Vieux comme le monde
Vitruve distinguait l’histoire de la construction de celle de l’architecture. La première, qui nous intéresse, s’attache à décrire les matériaux fournis par la nature et l’usage qui en est fait : un art de bâtir, de mettre en œuvre qui s’est développé selon les régions et affiné avec le temps.
En France, de nombreuses activités anciennes liées à la production de ces matériaux ont perduré, par exemple, en Bourgogne avec la terre cuite. «La fabrication de tuiles plates dans la région de Pontigny, dans l’Yonne, est attestée dès le 12e siècle. Jules Aléonard a ainsi fondé sa tuilerie en 1872 sur la base de ce savoir-faire ancestral », explique Frédéric Didier (Wienerberger). Les tuiles sont toujours produites selon la méthode traditionnelle, bien que la robotisation soit intégrée au processus. «Beaucoup de tâches restent manuelles, comme le triage ou l’empilage, mais nous avons fait le choix d’allier la tradition de la production à la modernité des outils pour produire plus et mieux, dans le sens de la sécurité et du confort pour les collaborateurs », ajoute notre interlocuteur.
La culture du bois est séculaire elle aussi et constitue une spécificité française. Depuis Colbert et son code forestier de 1669, la France s’est engagée dans la sylviculture du chêne. À l’origine, ces grands arbres de haute qualité, bien droits et cylindriques, étaient destinés à la fabrication d’une flotte royale inébranlable. Depuis, leur utilisation en charpenterie, en menuiserie et, surtout, en tonnellerie ne s’est pas démentie. Philippe Gourmain, expert forestier, déclare : « Notre forêt française couvre aujourd’hui 30 % du territoire, soit environ 17 millions d’hectares, et cette surface a doublé en 200 ans. »
Des pierres et des hommes
L’un des matériaux les plus lourds et donc des plus coûteux à transporter est bien évidemment la pierre. Ainsi, chaque filon représente une zone géographique : la Saint-Maximin et l’Euville pour Paris, la Sireuil à Bordeaux, le tuffeau de Touraine.
D’autres filons historiques sont aujourd’hui épuisés, le cas français le plus notoire étant la fermeture des Ardoisières d’Angers en 2013. Les chantiers s’approvisionnent désormais, pour beaucoup, en Espagne où la production d’ardoises de Galice s’est intensifiée. Le groupe allemand Rathscheck Schiefer exploite quatre carrières à ciel ouvert et la plus grande mine d’exploitation mondiale, La Fraguina. De son côté, Cupa Pizarras détient seize carrières dont San Pedro, la plus ancienne encore en activité au monde (depuis 1892).

Mine d’ardoise espagnole La Fraguina : 3 km de descente pour atteindre l’exploitation. Salle souterraine de 25 m de hauteur et de 100 m de longueur. Photo : Rathscheck Schiefer
La main et le savoir-faire
Bien que la mécanisation et l’industrialisation soient passées par là, des savoir-faire continuent de se transmettre et de s’enrichir. Ainsi, le fendage des ardoises s’effectue toujours à la main, car cette opération n’est pas « robotisable », seule la main maîtrise l’effeuillage subtil de la pierre. D’autre part, l’art délicat de la cuisson est essentiel pour toutes les productions de terre cuite. Olivier Lafore (Edilians) expose : «Nos équipes ont une grande maîtrise des cycles de cuisson et des fours. Elles acquièrent un vrai ressenti de la tuile, produit chaud, tactile et affectif. »
Côté chaleur, les professionnels de la verrerie Saint-Just, dans la Loire, ne sont pas en reste. Dernière productrice de verre architectural soufflé à la bouche, l’entreprise transmet les secrets de cette fabrication manuelle selon le principe du compagnonnage. Une vingtaine de professionnels se partagent la production de quelque 12 000 m2 de verre par an. Héritiers des travaux de Louis Vicat au début du 19e siècle, les chaufourniers et les cimentiers ont également affiné leurs savoir-faire. À Saint-Astier, en Dordogne, le calcaire siliceux, matière première des chaux hydrauliques naturelles, est extrait de carrières souterraines, puis lentement cuit dans des fours traditionnels verticaux, au briquetage intérieur spécifique. Au cœur du massif de la Chartreuse, en Isère, l’entreprise Vicat exploite, dans sa cimenterie historique de La Pérelle, un double filon de calcaire argileux aux caractéristiques uniques qui permettent, par cuisson entre 500 °C et 1 200 °C, l’obtention du fameux ciment prompt.
Des productions durables ?
Si les process sont largement maîtrisés aujourd’hui et ont permis d’améliorer les conditions de travail des collaborateurs, les enjeux environnementaux viennent questionner nos modes de production. L’une des interrogations est la gestion des carrières. En France, depuis les années 1970, la préfecture délivre une autorisation d’exploitation, en général pour une trentaine d’années. Cette autorisation engage l’entreprise à respecter des normes environnementales et sociales et notamment les aménagements et réaménagements à prévoir en cours et en fin d’exploitation.
Olivier Lafore (Edilians) explique : « Après exploitation, nous remblayons nos carrières d’argile avec la terre arable initiale, des déchets inertes, nous replantons des arbres. Parfois, les municipalités récupèrent le site et le transforment en espace de loisirs. D’autres fois, un micro-environnement se crée, attirant des espèces endémiques qui avaient disparu, et que, par suite, nous protégeons.» En Espagne, l’extraction et l’exfoliation de l’ardoise nécessitent une hygrométrie constante. «L’eau nécessaire est utilisée en circuit fermé, puis réinjectée jusqu’à épuisement, décrit Erwan Galard (Cupa Pizarras)». L’eau, après décantation, regagne ensuite naturellement les nappes phréatiques tout en se déchargeant de ses poussières dans le sol. Dans le cas de l’ardoise, la pollution visuelle reste le facteur le plus déterminant. «Nous n’utilisons aucun produit chimique, mais nous abattons de véritables montagnes», déclare Sylvain Dugal (Rathscheck Schiefer). En réalité, il est très coûteux de « reconstituer » la montagne où il n’y en a plus…
Des essences menacées ?
Forte de ses trois siècles d’expérience, la sylviculture française a fait ses preuves. Aujourd’hui, c’est encore et toujours le réchauffement climatique qui pose problème. «On récolte environ la moitié de l’accroissement naturel, donc, chaque année, la forêt augmente en volume. On ne peut pas dire qu’elle soit menacée», affirme Philippe Gourmain, expert forestier.
Cependant, certaines essences le sont, comme l’épicéa, qui commence à souffrir de la chaleur dès 600 m d’altitude. Les experts réfléchissent à l’introduction d’essences sudistes par l’intermédiaire d’une migration assistée. «Les espèces bougent naturellement, mais lentement, de l’ordre de 500 m par an pour le chêne, soit 500 km par millénaire… Ce n’est pas suffisant par rapport au changement climatique que nous vivons. Si nous ne les aidons pas, les essences ne monteront pas assez vite et, localement, pourraient disparaître », développe le spécialiste.
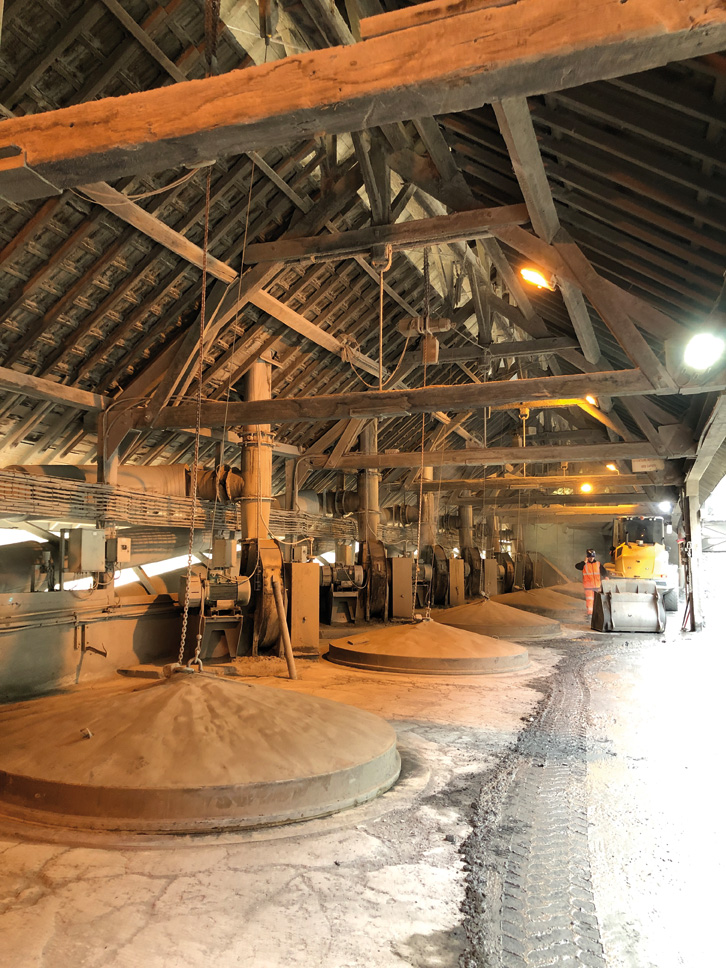
Les fours de cuisson de la cimenterie de La Pérelle (Vicat), créée en 1875. Photo : Opus M

Tuiles canal « vertes » avant cuisson, empilées dans l’usine de Castelnaudary. Photo : Terreal/Lulu
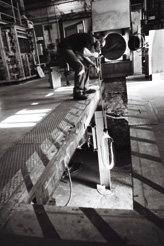
Le verrier souffle la matière en imprimant un mouvement de balancier dans le vide pour transformer la boule de verre en cylindre parfait. Sphère qui sera ensuite coupée par le fendeur et déroulée par l’étendeur pour obtenir une feuille de verre plane. Photo : Verrerie de Saint-Just
Gérer les énergies
Toutes les productions liées à la cuisson sont très vigilantes quant à leur consommation d’énergie. Généralement, les fours fonctionnent au gaz. Simon Ballagh (Verrerie Saint-Just) explique : «La technique ancestrale de production du verre soufflé à la bouche n’a pas changé, mais les outils et process ont évolué, notamment pour améliorer les rendements énergétiques. Tous nos fours ont été changés dans les années 2010 pour réduire les consommations d’énergie, ce qui nous a demandé un gros investissement.»
De la même manière, Éric Risser (Terreal) confie : «Nous consommons de l’énergie pour cuire nos produits, énergie dont nous essayons de réduire la quantité. Plusieurs leviers sont actionnés : l’amélioration des process via les équipements et l’optimisation de l’énergie, comme la récupération de la chaleur de cuisson pour la phase de séchage des tuiles. Enfin, nous recourons aux énergies alternatives, comme le biométhane, biogaz épuré issu des déchets ménagers. » Certaines usines misent aussi sur le photovoltaïque ou la biomasse pour diversifier leur portefeuille énergétique. Cependant, pour les produits destinés au patrimoine, il est compliqué d’optimiser totalement car certaines tâches doivent rester manuelles, les process sont difficilement perfectibles.
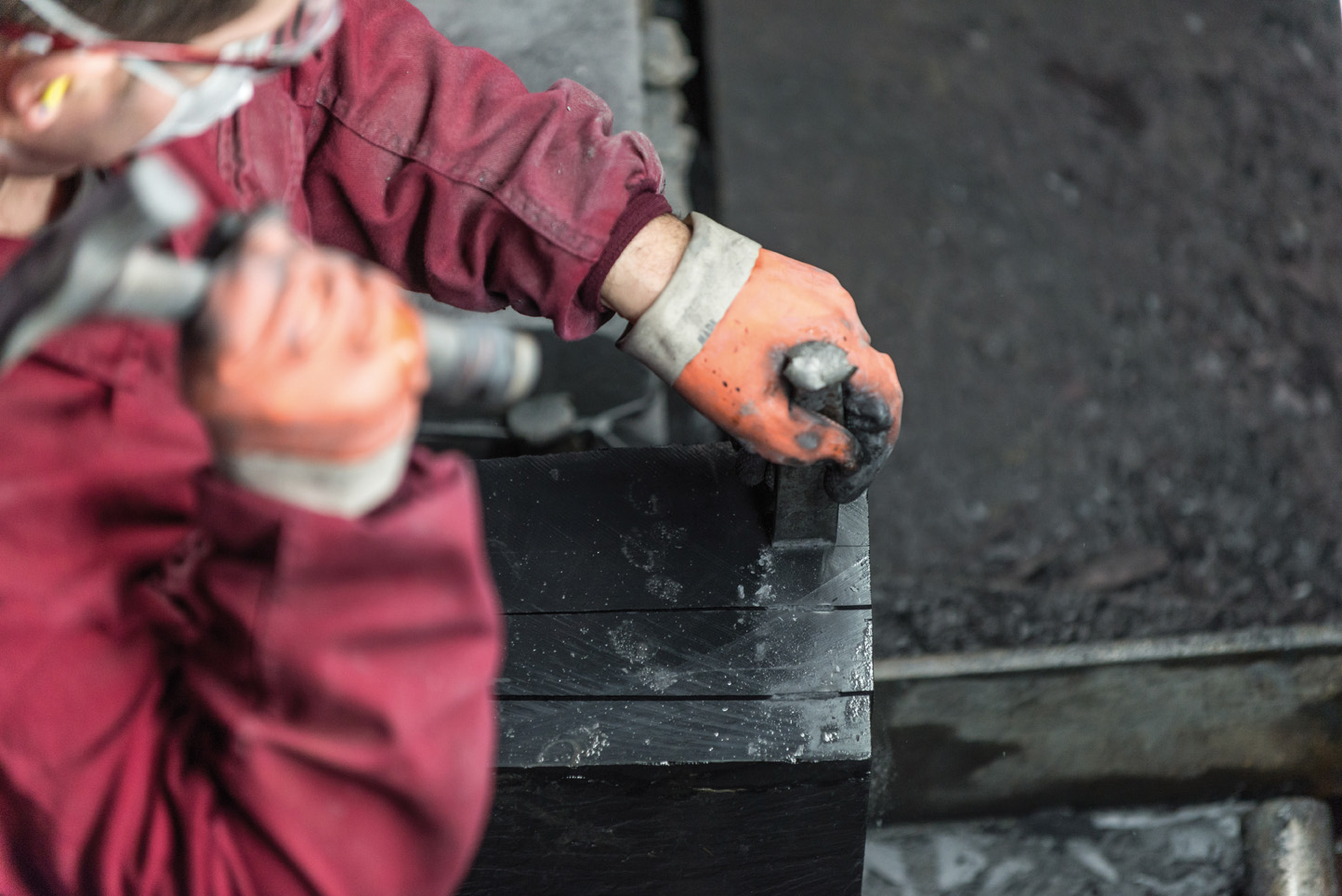
Le fendage des ardoises est réalisé manuellement par environ 200 maîtres fendeurs. Chacun d’eux réalise quelque 6 000 pièces par jour. Photo : Cupa Pizarras

Tuiles Aléonard après cuisson. Photo : Wienerberger
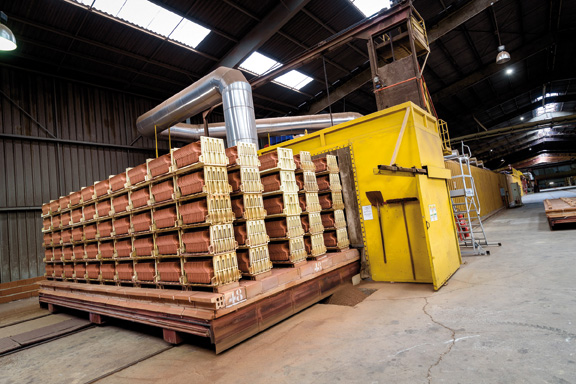
Four de cuisson des tuiles. Photo : Edilians
Certaines usines misent aussi sur le photovoltaïque ou la biomasse pour diversifier leur portefeuille énergétique. Cependant, pour les produits destinés au patrimoine, il est compliqué d’optimiser totalement car certaines tâches doivent rester manuelles, les process sont difficilement perfectibles.
Les industriels s’orientent vers l’écoconception de nouveaux produits : «C’est plus facile quand on commercialise un nouveau produit : on cherche dès le départ les solutions pour avoir le moins d’impact. On travaille sur son poids, sur son emballage (palettes recyclées), sur sa conception, etc. », poursuit Éric Risser (Terreal). Malgré les efforts opérés, les procédés industriels conservent une empreinte certaine sur l’environnement. Un des intérêts essentiels des matériaux du patrimoine est leur réemploi jusqu’à la fin de leur vie : l’intérêt de la filière est l’économie du matériau par la réutilisation et la réparation.
Aujourd’hui, pour tous les professionnels qui mettent en œuvre ces matériaux, il est essentiel d’avoir conscience de ces process de fabrication impactants. Il faut tout de même rappeler que la construction neuve reste la plus consommatrice de matières premières, comme le sable utilisé pour le béton qui contribue à l’érosion du littoral, et d’énergie.
Orianne Masse
Merci à nos interlocuteurs :
Frédéric Didier, directeur général adjoint, Wienerberger
Philippe Gourmain, expert forestier
Olivier Lafore, directeur marketing et communication, Edilians
Erwan Galard, responsable marketing, Cupa Pizarras
Sylvain Dugal, prescripteur, Rathscheck Schiefer
Simon Ballagh, directeur de la Verrerie Saint-Just
Éric Risser, directeur marketing, Terreal